- overview
- application area
- equipment features
Chemical Blend Unit: Precise Mixing for Production Requirements
The Chemical Blend Unit traces the process of mixing different chemical substances to produce a new mixture or solution. This may be done by manual- or automatic dosing and by weighing when using pumps or stirrers. Chemical mixtures may consist of several components, being combined in specific proportions for achieving an expected composition. Chemical mixing systems are important in many fields of chemical- and semiconductor industries because they are essential for the manufacture of their products.
Precise Mixture
A chemical mixing system enables the precise dosing and mixing of chemicals. By precisely controlling volume ratios and mixing parameters, analytical chemists can achieve the desired reaction conditions, thus improving the manufactured products´ quality.
Repeatability and Reproducibility
A chemical mixing system targets the repeated and reproducible mixing-processes. This is particularly important for the production of chemicals in large quantities or for the reproducibility, of for experiments and studies.
Efficiency Increase
By deploying a chemical mixing system, workflows will be optimized and thus increase in efficiency. Automated mixing processes reduce the manual workload and thus allow mixing processes to be executed more quickly.
Time and Cost Savings
A chemical mixing system may result in significant time and cost savings. Automated dosing and mixing of chemicals reduces failures, minimising material consumption. This fact offers a shortening of production and research times, resulting in an overall cost reduction.
Improved Safety
Deploying chemical mixing systems will reduce potential safety risks. The automated mixing process immediately reduces the contact with hazardous chemicals and this also reduces the risk of spills, vapours or other accidents.
Scalability
A chemical mixing system can be easily adapted to different requirements and production volumes. This offers the scaling of mixing processes, from small laboratory scales to industrial production facilities.
Applications of Chemical- and Slurry Mixing Systems in Industry
Chemical- and slurry mixing systems are deployed in various fields, especially in industries where the mixing of chemical substances or suspensions (liquids with solid particles) plays a crucial role in the production process.
Standard Functions
- Mixing tank and daytank placed inside the cabinet or externally
- Fully automatic pump switching function for uninterrupted chemical feed
- Automatic system shutdown by hardware safety interlocks
- Pressure monitoring and regulation of the supply-line, from the supply-tank to ensuring constant pressure at the point of use.
- Redundant pumps and filters possible
- Automatic pump and filter venting when required
- Manual flushing and cleaning of the system
- Monitoring of filter service life via differential pressure monitoring upstream and downstream of the filter
- Nitrogen overstocking of chemicals inside the drums or containers, if required.
- UPW or UN2 spray gun
- Additional pressure sensors for auxiliary media in the pneumatic system
Control Panel
- Siemens SIMATIC S7 series PLC
- Siemens SIMATIC Comfort Panel HMI
- User authorization and password protection HMI
- Multilingual operating instructions on the HMI
- Manual operation of pneumatic valves
- Linking with a monitoring and
- Data acquisition system for controlling the system
- Access for service and maintenance via remote control module
Safety Functions
- Insulated process and electrical casings
- CDA flushing function for the electrical casing
- Audible and visual alerts and warnings
- Local and remote EMO (Emergency Off) detection of exhaust gas flow
- Leakage detection inside the casing
- Door locking system
- Failure Mode and Effect Analysis (FMEA)
Options
- Vibration dampers, stroke counter and leakage detection for diaphragm pumps
- Chemical recirculation
- Temperature monitoring
- Daily tank capacity up to 2000 l inside the cabinet
- Automatic chemical quality analysis during delivery (optional online measurement technology)
- Day-tank housing
- High-precision radar sensor for level monitoring of the day-tank
- Measurement of pressure and flow at pump outlet
- Consumption monitoring
- FM4910 fire protection plastic casing
- Automatic system flushing and cleaning
- Platformscale below the mixing tank for the accurate measurement of the mixture
You may also find these topics interesting
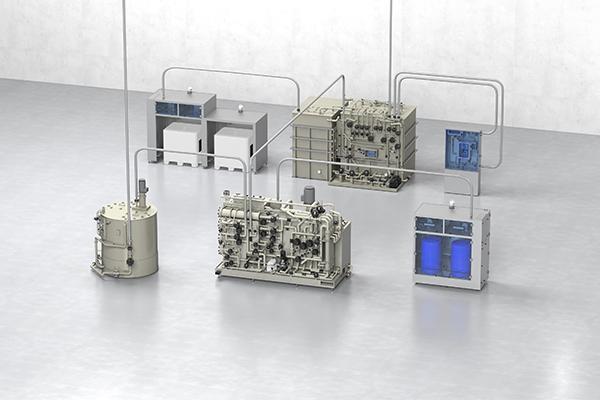
HighQ
The future of the semiconductor industry is here to find: Faeth Group’s patented recycling plant for environmentally friendly slurry raw material recovery!
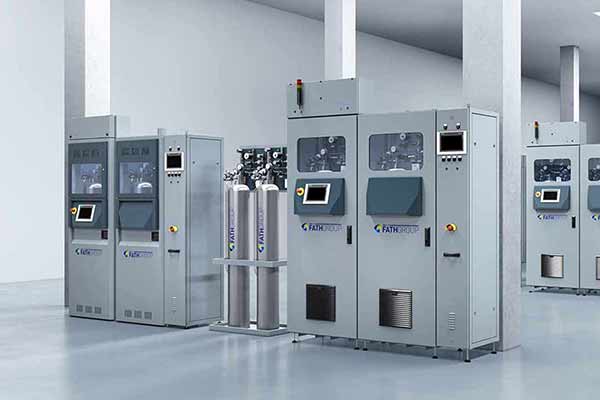
Gas support systems
Experience the innovative Gas Support Systems by Faeth Group for the industry, pharma & lab – perfectly adapted to your requirements.
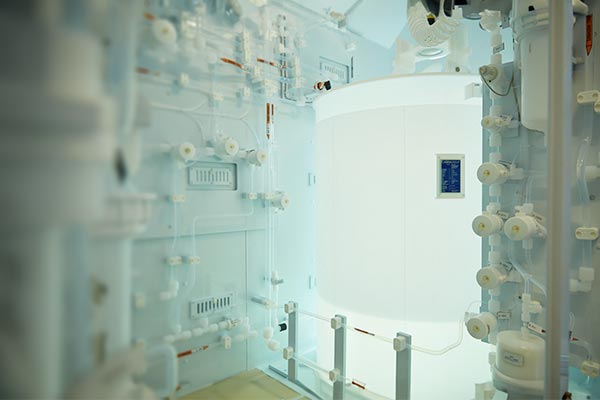
OEM Contract Manufacturing
Increase your productivity with our OEM contract manufacturing. Learn more about our matching solutions!